The 2019 edition of Solar Power International (SPI) rallied the North American solar and storage community in Salt Lake City, where industry pros enthusiastically participated in the usual combination of packed exhibit halls, engaging conference sessions, and entertaining after-hours networking events. Some of the hot topics at the show were obvious – the bifacial PV buzz, smart(er) energy storage integration, the federal Investment Tax Credit (ITC) extension push, for example – while other important trends kept a lower profile. One of those subtler mission-critical topics falls right in PVEL’s wheelhouse: the growing emphasis on product quality and reliability across the value chain.
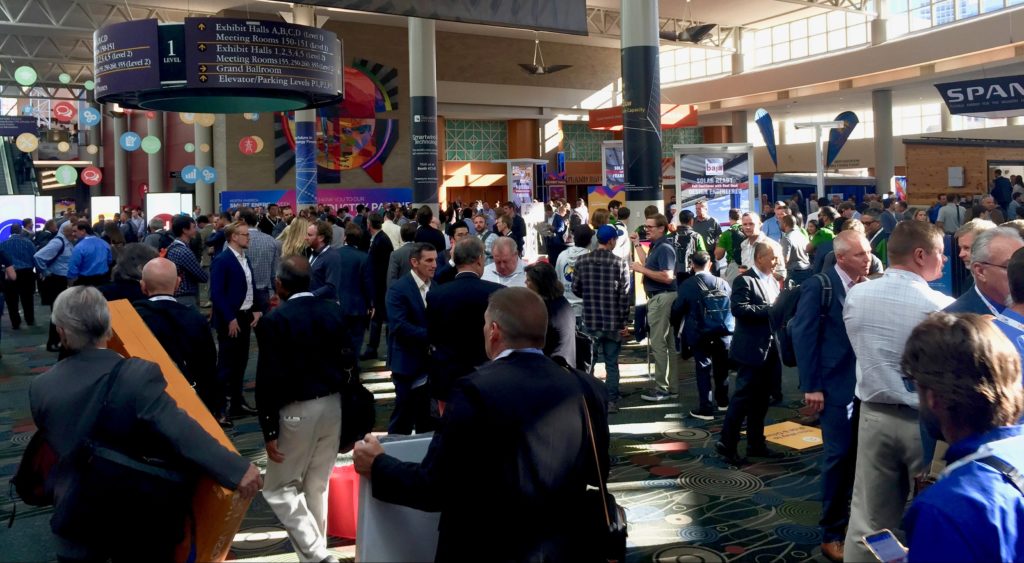
The Salt Lake City Convention Center was full of networking solar professionals on the first day of SPI.
One of the SPI events where the PVEL team spread the word about quality, reliability and performance was pv magazine’s pair of roundtables themed around the future of PV and quality issues. CEO Jenya Meydbray, Head of PV Module Business Tristan Erion-Lorico and I participated in the lively discussions.
When Jenya gets to talk about PV technology and its future, he’s in his element. While much of his panel’s conversation focused on emerging PV technologies like heterojunction cell architectures and tunnel-oxide passivated contact layers, there were a few quality and reliability takeaways that transcended the innovations themselves.
Jenya noted that with the introduction of each exotic cell technology, new and possibly unforeseen aging and degradation behaviors appear, and that people may not appreciate these behaviors until they’re seen in the field. He cited the example of light and elevated temperature induced degradation (LeTID), which has cropped up in the popular PERC cells. The behavior results in as much as 7% degradation of module performance after only one year in the field. Although the root cause of LeTID has yet to be determined, manufacturers have added stabilization processes to their production lines in an attempt to control the degradation mechanism.
During the discussion of one of the hottest module topics—bifacial PV—Jenya explained that there are more far-reaching implications with this technology than just the dual-sided energy-generating abilities of the modules themselves. For the first time, the introduction of a new cell/module technology requires a thoroughly integrated system design involving the module, tracker, inverter and the balance of system. This means that for bifacial modules there are far more nuances at the design level than ever before, from measuring for LeTID and other degradation on both sides of the modules to design and installation considerations like tracker torque tube stress factors, and the impact of the weight and size of the glass-heavy modules on labor costs and shipping. As he pointed out, it’s actually easier to build a bifacial system than to optimize it.
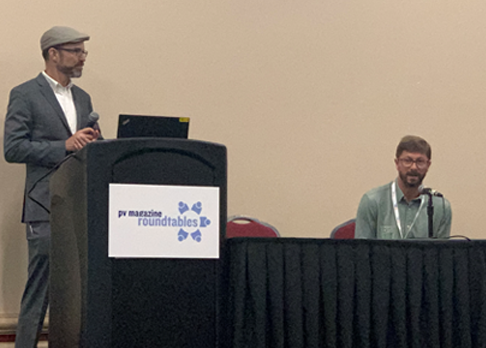
PVEL CEO Jenya Meydbray at pv magazine’s Future of PV roundtable.
I was part of a panel about the crucial need to ensure bill of materials (BOM) quality. Know- your-BOM is one of PVEL’s mantras, so I emphasized the importance of selecting quality materials that will better ensure the long-lasting life of your PV and storage components and therefore your assets. I also mentioned the best practice of knowing the factory where your BOM is produced and specifying those materials in your supply contracts, as well as monitoring the manufacturing process during project construction.
A discussion around backsheet failure mechanisms allowed me to talk about PVEL’s new backsheet durability sequence, which was added to our Product Qualification Program (PQP) this year at the insistence of the PV module buyer and asset owner community. So far, we’ve seen a wide range of results while stressing the modules, with some coming through the three-cycle sequence with no signs of backsheet cracks, while others reveal cracks after one or more cycles.
Tristan presented a case study—actually more of a cautionary tale—of module underperformance at a 10 MW site in California originally built in 2011. When the new owner purchased the plant in 2016, they uncovered significant issues with some of the modules. After taking a deep dive into the situation, eventually with the help of a Heliolytics aerial thermal scan, the asset owner determined that half the site’s modules suffered from microcracks caused by poor cell-busbar soldering practices at the factory.
Here’s where the cautionary tale part of Tristan’s case study comes into play. Back in 2011, PVEL did statistical batch testing for modules to be installed in that 10 MW project in California. Although most of the samples exhibited signs of excessive microcracking due to poor soldering, PVEL’s results were not fully considered by the original owner and the module installation proceeded.
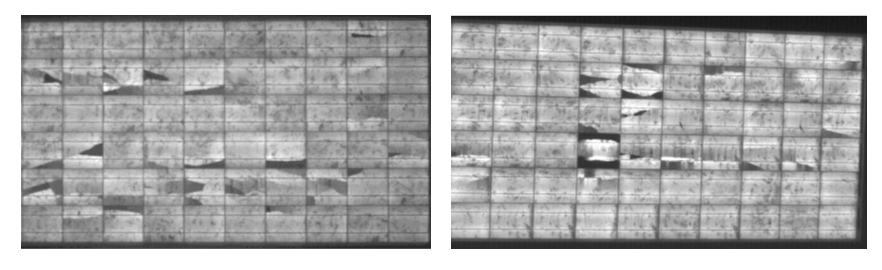
The EL image on the left of a microcracked PV module was taken during PVEL’s statistical batch testing for the 10 MW project. The EL image on the right shows a PV module from that project with excessive microcracking after just five years in the field.
Finally, our new partnership with Heliolytics proved to be one of the most exciting announcements issued at SPI. Our companies have teamed up to offer an Incident Response service that combines advanced aerial imaging and field testing to help stakeholders quantify damage to—and mitigate financial losses in—solar power plants after natural disaster events. For example, one of the benefits of the service for insurance companies is that the testing after a serious weather event may indicate that they only have to replace a portion of a solar field, rather than 100% of the modules and other equipment. There was plenty of interest in the program at the Heliolytics booth and around the show, including coverage from various solar trade media outlets.
In short, PVEL had a great and productive SPI 2019. I want to thank the show organizers, exhibitors and attendees for their efforts and enthusiasm. The event is impactful for solar companies across the value chain; SPI brings the industry together for discussion and debate on the topics that matter most to our future growth. I’m pleased that product quality and reliability are now consistent themes in the broader conversation, show after show. We look forward to next year’s SPI in Anaheim!