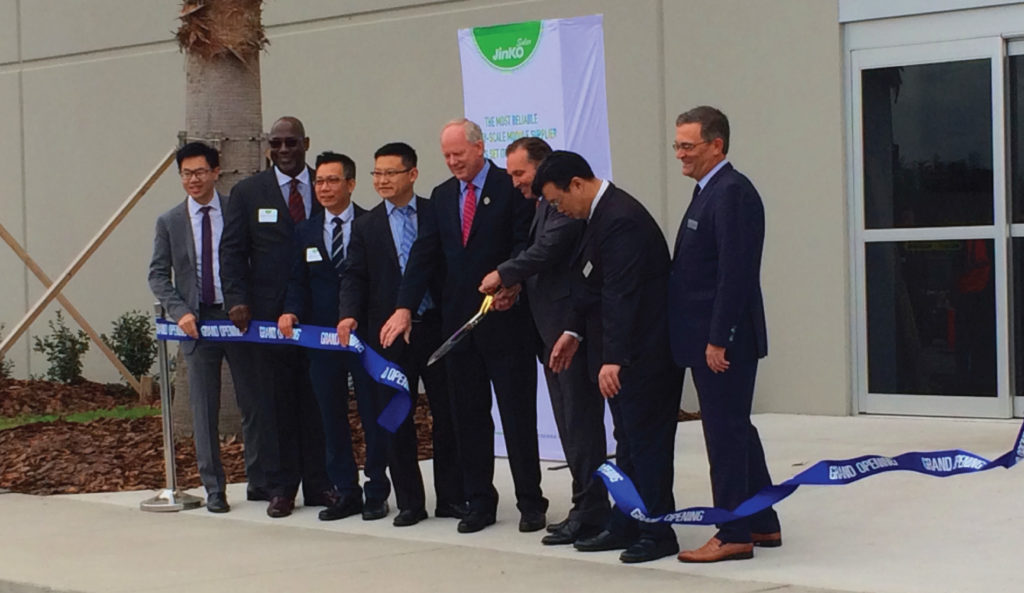
JinkoSolar recently made headlines with the grand opening of its 400MW solar module factory in Jacksonville, Florida. In this article, I’ll share impressions from my tour of the new production facility.
While PVEL has not yet tested the modules produced in JinkoSolar’s new factory, it was clearly designed as a showcase for advanced PV module production. JinkoSolar is also a four-time Top Performer in our PV Module Reliability Scorecard. How do their new “Made in America” modules compare to the modules they produce in China, Malaysia and Spain? How will they perform relative to U.S.-made products from companies like Silfab, Sunpower and Hanwha?
Without rigorous, independent testing, there’s no way to answer these questions with confidence. However, data from nearly ten years of independent testing at PVEL demonstrates that factory location does not impact PV module reliability or performance. The main drivers of product quality are Bill of Materials (BOM) and manufacturing processes, not country of origin.
In other words, it’s possible to produce a top-quality PV module anywhere in the world with the right materials, tools, procedures and personnel – and mismanaging any one of those factors can cause serious problems.
Advanced Module Manufacturing in the U.S.
JinkoSolar’s fifty million USD factory was built in partnership with local authorities. All told, it’s a boon for American manufacturing. Six hundred fifty local laborers were employed to build it, and the company is slated to employ around two hundred factory workers by the end of this year. The facility is designed to produce two monocrystalline PERC modules every minute, around the clock.
To celebrate, JinkoSolar brought together local stakeholders as well as the company’s top partners, clients and affiliates for a ribbon cutting ceremony and tour. The factory was constructed as a show piece; the work areas are enclosed behind glass walls and an interior, but an outer perimeter provides visitors with a path to walk around the factory floor and observe production.
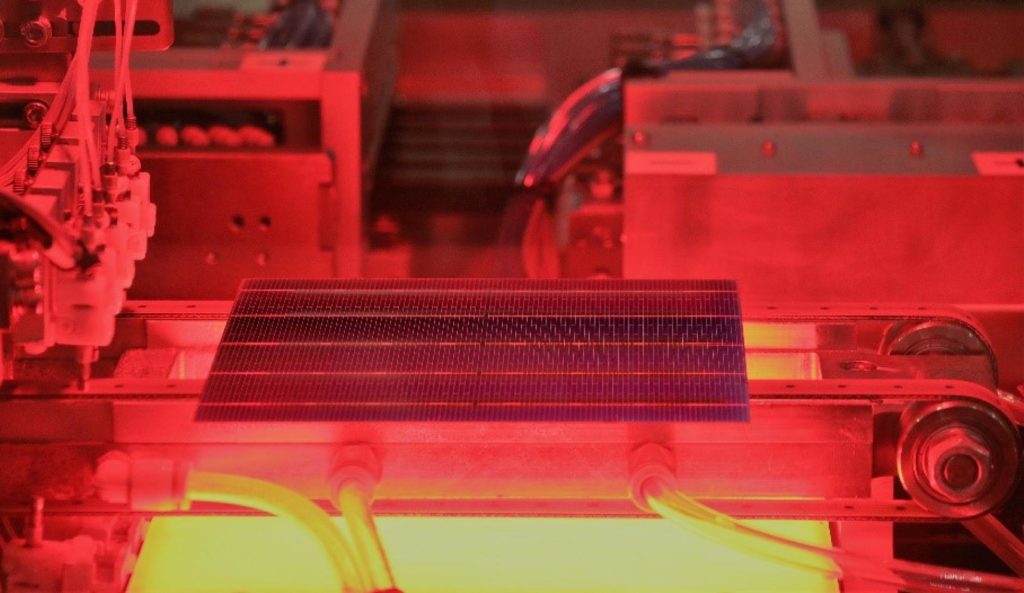
The level of automation at JinkoSolar’s Jacksonville factory immediately captured the attention of everyone in my tour group. For example, junction boxes are adhered to the module’s backsheets using cranes equipped with suction cups. These cranes transport modules from one piece of machinery to the next. Ideally, this eliminates the potential for operator errors that could damage backsheets or cause microcracks in cells. JinkoSolar also plans to use artificial intelligence (AI) to review electroluminescent (EL) images taken during production.
Automation Does Not Guarantee Module Reliability
Highly automated equipment and processes can expedite production and drive down manufacturing costs substantially, so we’re excited to see it in the U.S. But it’s not a fool-proof way to eliminate defects. Unless equipment is calibrated and pre-sets are validated on a regular basis, automation and AI can miss major issues. These tools are only as effective as the operators who program the algorithms and check machinery. Defects that pass through automated quality control checks without operator inspection could easily impact a large quantity of product produced, so diligent inspection is critical. A human eye should validate product quality at every station in the automated process.
New factories, new process, new automation, new operators, and new quality managers can all be factors contributing to the performance of a particular product line or BOM.
That’s why the best way to determine if a manufacturing facility will produce a quality product is to conduct an independent factory witness. Every component and material that goes into the module will be inspected by an independent third party at every step of production. (PVEL’s Product Qualification Programs, or PQPs, require a factory witness every eighteen months.)
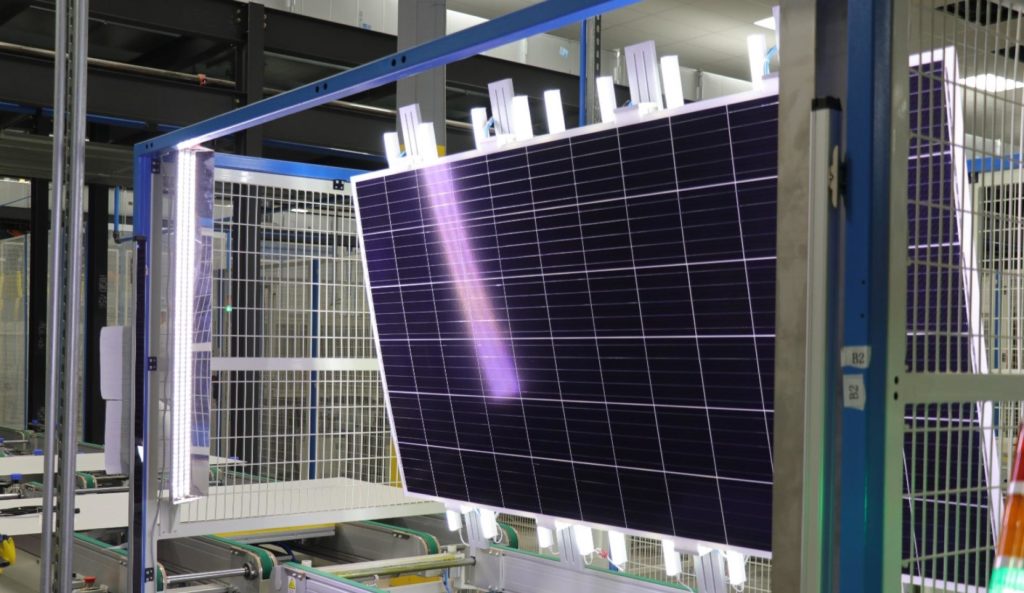
One thing’s for certain: This new factory will help JinkoSolar and NextEra – that’s the parent company of Florida Power and Light and one of Jinko’s top customers – avoid costly import tariffs. JinkoSolar is among the first Chinese PV module manufacturers to invest in new manufacturing capacity in the U.S. In the long-term, its new factory promises to deliver significant benefits for all of its U.S.-based clients, not only NextEra. Their new Jacksonville factory could even become an icon of American PV manufacturing.
But as with any PV module factory and producer around the world, savvy buyers should inspect and test before they invest.
We look forward to opportunities to test the modules JinkoSolar produces in Jacksonville as well as products from other manufacturers opening new factories across the U.S. and around the world.